A Comprehensive Guide on Six Sigma Tools and Techniques
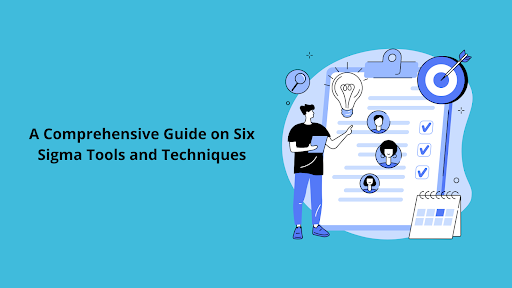
Sigma Tools: Efficiency, effectiveness, and innovation are essential in a dynamic business environment to stay ahead of the competition. Many people have frequently run upon the phrase “Six Sigma Certification” and wondered, “What is Six Sigma?”
By locating and removing the root causes of errors and reducing variability in production and business processes, Six Sigma is a systematic approach to process improvement. It employs a variety of tools and methods to raise quality, cut waste, and increase profit. In this blog, we’ll look at the basic Six Sigma tools and methods that have changed how many industries look.
Table of Contents
- DMAIC Methodology
- Fishbone (Ishikawa) Diagram
- Pareto Chart
- Process Mapping (Flowcharts)
- Statistical Process Control (SPC) Charts
- Control Charts
- Design of Experiments (DOE)
- FMEA (Failure Modes and Effects Analysis)
- Voice of the Customer (VOC)
- Hypothesis Testing
- 5 Whys Technique
- Conclusion
DMAIC Sigma
DMAIC defines the five stages of a Six Sigma project: define, measure, analyse, improve, and control. This framework offers a step-by-step method for improving processes and solving problems:
- Define: Understand and describe the problem.
- Measure: Collect relevant data on the current process.
- Analyse: Evaluate the data to identify the root causes of defects.
- Improve: Develop, test, and implement solutions to the issues.
- Control: Monitor the solutions to ensure they’re sustainable.
Fishbone (Ishikawa) Diagram
This tool aids in locating probable process failure reasons. Think of the “spine” as the issue and the “bones” that branch off as probable reasons as the skeleton of a fish. Teams can more precisely identify the issues that require attention by brainstorming and classifying these causes.
Pareto Chart
The Pareto Principle, sometimes called the 80/20 rule, argues that just 20% of causes account for 80% of issues. A Pareto Chart is a sort of bar chart that lists the causes of issues in order of importance. Teams may prioritize the most important problems first with the help of this visualization.
Process Mapping (Flowcharts)
One must first visualize a process in order to comprehend and enhance it. Teams can find bottlenecks, duplicate stages, or possible error spots in a process by using flowcharts, which are frequently used in process mapping. For more details click here Is Kisskh.me Down.
Statistical Process Control (SPC) Charts
SPC graphs track a process’ performance over time. They can show how much variance there is and whether the process is still within allowable bounds. SPC graphs are essential for verifying a process is stability after making changes.
Control Charts
Control charts, a particular variety of SPC charts, display data points sequentially while emphasizing the mean and control boundaries. Teams can use it to spot patterns, alterations, or cycles that could be signs of emerging issues.
Design of Experiments (DOE)
Finding the connection between the inputs and outputs of a process and the elements (variables) impacting those processes is done using a systematic, organized technique called DOE. Understanding which factors affect the outcome most aids in process optimization.
FMEA (Failure Modes and Effects Analysis)
A methodical strategy of locating and examining probable failure modes in a process is called FMEA. Each failure is ranked based on its significance and chance of occurring. Prioritizing areas that require attention or redesign is made easier by this approach.
Voice of the Customer (VOC)
Any business’s consumers are its lifeblood. Customer expectations, preferences, and aversions are captured via VOC. This priceless feedback assists in coordinating business procedures to meet or surpass client expectations.
Hypothesis Testing
Making data-driven judgments is aided by hypothesis testing, which establishes whether an observed change or difference is meaningful or merely a result of chance.
5 Whys
The 5 Whys is a simple problem-solving technique that asks “Why?” (usually five times) to get to the bottom of a problem. It’s straightforward yet quite powerful.
Conclusion
Six Sigma has earned a position in process optimization and quality control thanks to its abundance of tools and approaches. Understanding these tools is essential whether you’re considering earning a Six Sigma certification or are just intrigued about its methodology. Although tools are essential, keep in mind that the actual game-changer in Six Sigma is the concept, which emphasizes continual development and a dedication to quality. Organizations may optimize operations, save waste, and provide extraordinary value to their consumers by utilizing these tools and strategies.